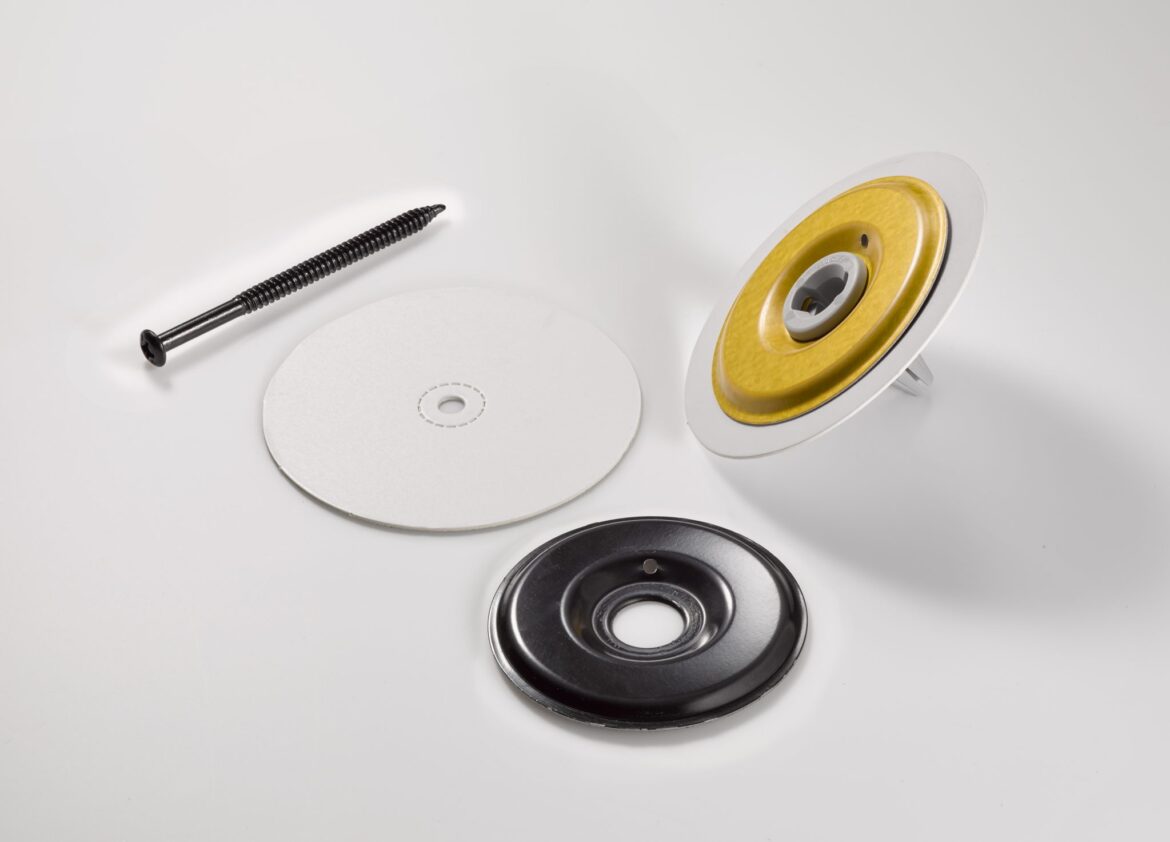
Roof Insulation Simplified with Cardboard Disks for Induction Welding
Demand for high performance roofing is on the rise as heating and cooling costs continue to increase. To create energy-efficient roofs, contractors have chosen expanded polystyrene (EPS) insulation for its ability to block heat loss and heat gain in buildings.
During traditional installation in roof assemblies using TPO or PVC membranes, fasteners are screwed into the roof deck through the membrane and EPS. Piercing the membrane with fasteners may allow moisture intrusion through the holes that are created in the membrane.
As an alternative installation method, roofers turn to induction welding.
Induction Welding Process
Induction welding is used to prevent the penetration of fasteners through the membrane. During this process, crews attach the insulation using screws and 2-inch diameter plates. After the fasteners are secured, the membrane is unrolled over the insulation and fasteners. With the membrane in place, an induction welding tool is placed over each plate location and rapidly heated to about 500° F, which bonds the membrane to the plate.
Induction Welding and EPS
Induction welding is not a new method of securing roofing membranes to rigid insulation; although the process has historically been difficult to use with EPS insulation assemblies. During induction welding, EPS foam would depress from the heat if the foam did not have a cover board. These depressions in the EPS would allow water to pond and eventually damage the roof. As a simple solution, fastener manufacturers developed a thin, moisture-resistant, compressed paper-based product known as an “induction welding cardboard disc.” These discs offer protection to the EPS from the induction welder, even in the absence of a cover board, without compromising the thermal bond with the membrane.
What This Means for Roofers
The simple installation of induction welding cardboard discs coupled with EPS provides roofers with a lightweight, low-cost and high-efficiency roof. EPS is available in varying sizes, including 200 square foot fanfold bundles, making it a viable option for rapid insulation coverage in a large area. Fanfold bundles also require fewer fasteners per square foot, which, when combined with the fewer fasteners required for induction welding, adds up to labor savings.