Originally posted on SitePrep online, March 2014
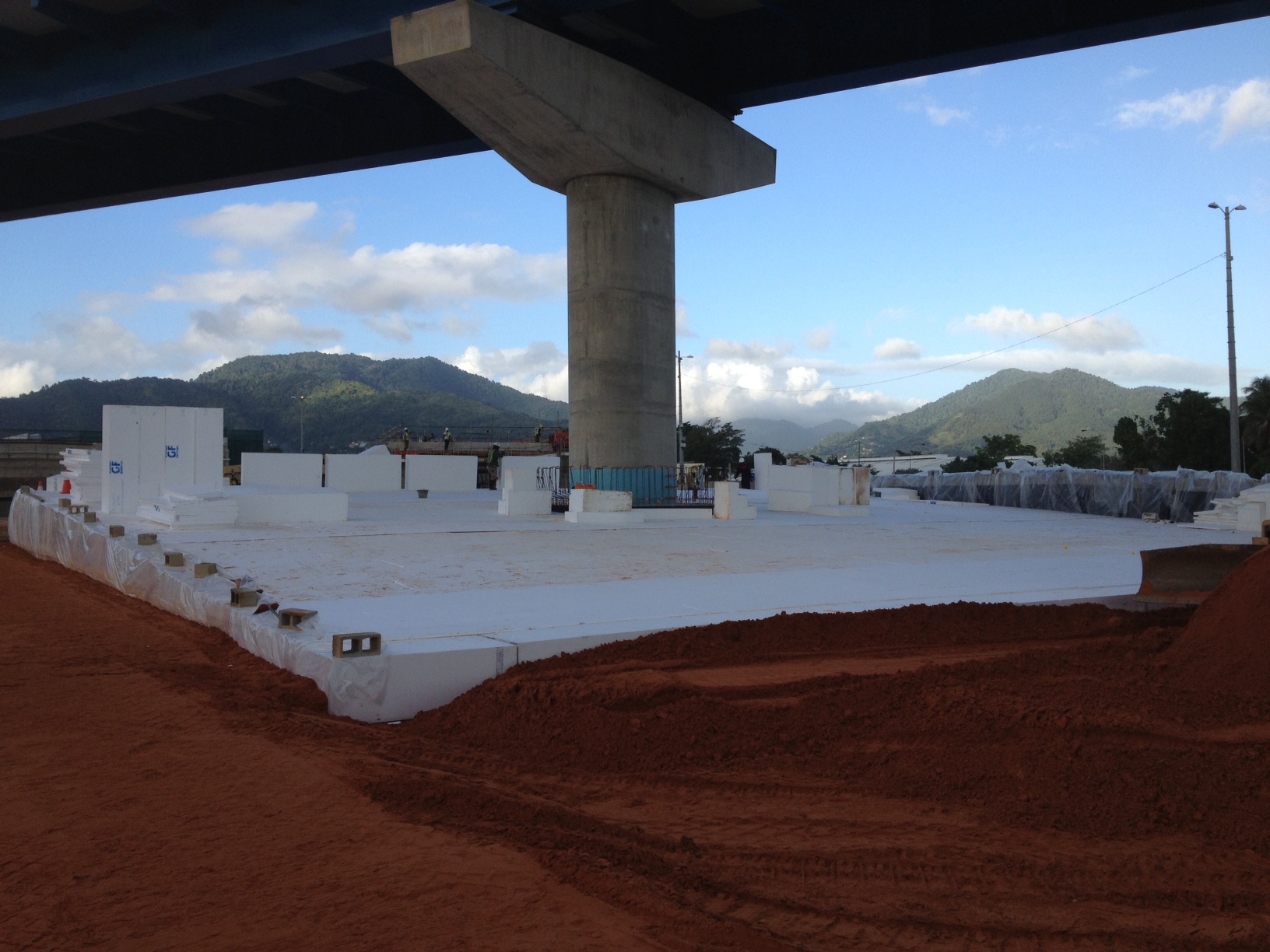
Working in the soft soils of Trinidad, the contractor specified EPS geofoam to reduce the load applied to the pile cap under the existing pier on this freeway interchange project.
Although greenfield site preparation can involve a host of geotechnical challenges, in urban areas the need to work around existing infrastructure presents its own costly and complex design problems.
A new freeway interchange at Valsayn on the Caribbean island of Trinidad provides a clear example of the potential difficulties. Traffic growth in the island nation required the development of a new grade-separated interchange between two primary highways – the Churchill-Roosevelt Highway (CRH) and the Uriah Butler Highway (UBH).
One challenge the project team faced was that the north and southbound lanes of the UBH needed to pass adjacent to (and on both sides of) a support column for an existing flyover ramp. The new lanes required pavement of 9.8 to 10.5 ft. of embankment fill on top of the pier’s pile cap on very soft soils. A concrete shaft of seismic activity. The concrete shaft also keeps the pier in depended for the the new fill.
Designing infrastructure to mitigate earthquake damage is crucial in Trinidad, which lies near the boundary of two tectonic plates. The island has been impacted by five earthquakes greater than magnitude 7.0 since the 1700s, including a 7.3 quake in 2007.
To reduce the load applied to the pile cap under the existing pier, and to avoid any modification of the pier’s seismic behavior, contractor Vinci Construction Grands Projects specified InsulFoam GF expanded polystyrene (EPS) geofoam as a lightweight fill. Goefoam offers high compressive strength and predictability, yet weighs up to 100 times less than traditional soil fills depending on the EPS density selected.
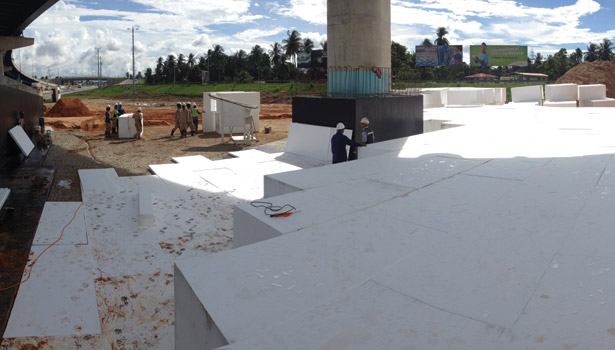
EPS geofoam fill provided a cost-effective alternative to building a concrete slab founded on piles to support the load from the road and transfer it away from the pier pile cap.
Vinci Construction Grands Projets crews placed 2,100 cu. yds. of EPS22 geofoam fill in an 80 by 89 ft. area surrounding the pier in only three-and-a-half days. “Because of the ease and speed of installation, using geofoam allowed us to build this fill two times faster than a regular sand fill, especially in Trinidad where heavy rains can interrupt back filling activities for days,” says Cecile Huillard, construction engineer with Vinci Construction Grands Projets.
Huillard notes the use of EPS geofoam fill provided a cost-effective and simple alternative to building a concrete slab founded on piles to support the load from the road and transfer it away from the pier pile cap. No heavy equipment was needed for the fill placement, as crews were able to install the geofoam blocks by hand. Additionally, the geofoam resulted in lower and smoother post-construction differential settlements of the roadway in both the transversal and longitudinal directions. The use of geofoam also eliminated the need for additional geotechnical investigation for potential additional piles.
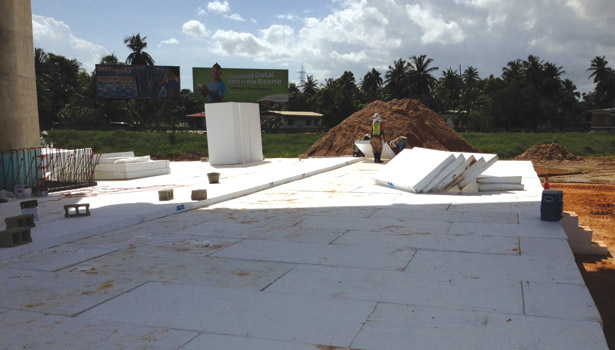
Using EPS geofoam as a lightweight fill reduces labor and material costs without the need for over-excavation.
EPS geofoam does not typically require surcharging, preloading or the staging often necessary with other fills. It resists moisture, freeze-thaw damage, insects, mold and decomposition. The product is inert, does not emit undesirable gases or leachates, and is reusable or recyclable. EPS geofoam is available in multiple strengths suitable for a wide range of engineered applications. The EPS22 geofoam specified in the CRH/UBH interchange project has a compressive resistance of 1,051 psf at 1-percent deformation.
In addition to soft soil remediation and reducing vertical loads on existing infrastructure and utilities, engineers have used EPS geofoam to solve a range of other geotechnical challenges, as outlined in the adjacent article, Applications for Lightweight Geofoam Fill.
Applications for Lightweight Geofoam Fill
Given EPS geofoam’s low weight, strength and ease of use, more project teams are using it to solve regular construction challenges in five basic applications:
1. Eliminate or reduce lateral loads on structures.
2. Create a zero loading factor for soft soil remediation.
3. Lighten the driving block of a landslide for slope stabilization.
4. Reduce lateral and dead loads over existing or newly buried utilities.
5. Use as lightweight structural void-fill for numerous concrete and landscaping applications.
STRUCTURE LOAD REDUCTION
EPS geofoam significantly reduces lateral loads on retaining walls and building foundations. The material has an extremely low Poisson’s ratio (.05) and high coefficient of friction (.6), which helps enable placement of blocks in a way that replaces the sliding soil wedge above the angle of repose. By replacing the active wedge with EPS geofoam, which can be completely freestanding and self-supporting, project teams can save up to 75 percent of total project costs compared to traditional concrete walls designed to retain soil.
Using EPS geofoam also reduces labor and material costs without the need for over-excavation, and requires much less robust forming, reduced structural steel and concrete wall thickness, and fewer footings. The material can also reduce or eliminate the need for geo-grids and/or mechanical tiebacks. Project teams are able to construct a retaining wall with EPS geofoam paired with a lower-cost fascia (which acts more like a fence).
Another key advantage of using the material in retaining wall applications is the allowance for taller walls in narrower rights-of-way. This reduces time and cost spent on property acquisition, as well as minimizes lane closures and encroachment into wetlands or neighboring properties.
SOFT SOIL REMEDIATION
Ground with soft soils or soft clay makes construction difficult. These soft surfaces are notoriously poor foundations for many projects, and can require extensive remediation.
Instead of choosing costly (surcharging) and time-consuming remediation of soft soils, projects of all sizes can install EPS geofoam, which provides high load-support while maintaining a low weight.
SLOPE STABILIZATION
EPS geofoam’s low weight makes it an excellent option for stabilizing steep slopes, without the need to change the final slope geometry. As the material is much lighter than other fills, it greatly reduces the weight of a slope’s driving block and lowers the risk of costly and dangerous slope failures.
Additionally, since slope stabilization generally happens on steep and uneven terrain, using EPS geofoam simplifies construction, because crews can move and place it without heavy earthmoving and compaction equipment, thus greatly speeding up the construction schedule.
UTILITIES LOAD REDUCTION
Throughout the world, existing buried utilities create challenges for new construction. Notably, utilities frequently are not designed to have additional loads placed upon them. So, utilities either have to be moved or upgraded at high expense.
Instead, geofoam can be an ideal option to reduce dead and lateral loads on underground pipes, culverts and tunnels, while at the same time providing high thermal insulation values that protect against temperature fluctuations.
Another advantage is geofoam can protect utilities during seismic activity by reducing in-situ vertical/lateral stresses.
STRUCTURAL VOID FILL
Given its low weight, EPS geofoam is also well suited as a structural void fill in concrete forming operations. Crews can easily fabricate virtually any shape or slope, and the material eliminates separate concrete pours for vertical wall sections and topping slabs.
Applications include bridge column formwork, stadium seating in auditoriums and sports arenas, stairways, podiums, loading docks and rooftop pool decks. EPS geofoam can be manufactured into custom-cut blocks in various shapes and sizes to enable contractors to quickly build up these and other similar features.
“Because of the ease and speed of installation, using geofoam allowed us to build this fill two times faster than a regular sand fill, especially in Trinidad where heavy rains can interrupt back filling activities for days.” – Cecile Huillard, Construction Engineer, Vinci Construction Grands Projects