How EPS Insulation Can Help Address Today’s Residential Building Industry Challenges: Labor Shortages & Material Costs
2020 was a year like no other—in more ways than one. The housing market collectively experienced a suburban shift, with a “fueling investor interest in build-to-rent (BTR) communities as millennials flee apartment buildings,” according to Builder magazine.
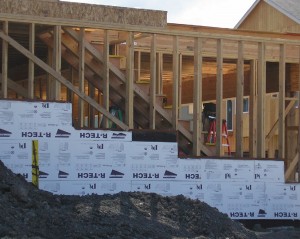
Insulfoam’s ENERGY STAR® certified R-TECH Insulation Panels used on a new residential construction project.
To meet this “near insatiable demand for single-family housing,” it’s more important than ever for building professionals to turn to efficient building products that optimize labor resources and reduce overhead amid rampant fluctuations in the cost of building materials. Employing labor-saving measures is particularly imperative, given that the “industry’s labor shortage is expected to get worse, as retirement beckons to a sizeable percentage of the U.S. construction workforce,” said the president and CEO of the Home Builders Institute in a recent Bloomberg feature.
To keep single-family construction timelines in pace with demand despite the labor shortage and fluctuating building material costs, professionals can turn to expanded polystyrene (EPS). Keep on reading to learn how EPS can help address today’s most pressing residential building industry challenges.
EPS’ versatility addresses residential building industry challenges by providing labor and material-savings
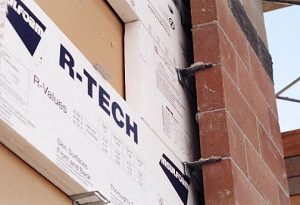
R-Tech Panels are an engineered rigid insulation consisting of expanded polystyrene (EPS) with advanced polymeric laminate facers
EPS’ lightweight composition, in combination with its compressive strength and exceptionally high R-values, can support substantial labor and material-savings. The versatile material can be employed across walls, floors, the foundation and attic for high-caliber insulation. Engineered to maximize operating efficiencies for smaller crews, the factory-cut, custom-built EPS panels call for less material handling, don’t need to be cut once on site and can be installed easily and efficiently by hand due to their lightweight nature.
While lightweight, the rigid foam material is also engineered to demonstrate impressive compressive resistance to support high loads. For foundation and wall applications, the foam insulation can effectively absorb movement without transferring stress to the interior or exterior finish at the joints. Similarly, the material also provides dimensional stability across residential roofing applications and can support the weight of roof traffic or equipment. Easily customizable, EPS manufacturers can increase the density of the product to meet virtually any compressive strength requirement. With this level of brawn, residential building professionals can meet project goals with fewer layers of insulation. Less material in play helps simplify construction logistics, slimming labor and material costs.
EPS’ superior thermal performance also plays a role in keeping residential projects on schedule and on budget, as it’s possible to achieve the architect’s specified R-value without the added labor or material costs that are typically associated with building up multiple layers of insulation across a building envelope.
Final thoughts
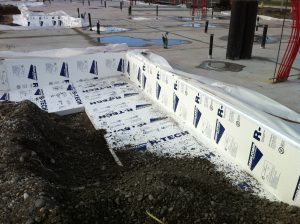
R-TECH Insulation Panels used in a below-grade application.
EPS offers residential building professionals a versatile, economical insulation product. The rigid foam material exhibits several special characteristics—a lightweight composition, exceptional compressive strength and high R-values—that truly sets it apart from comparable insulation solutions.
To learn more about how EPS can help address today’s residential building industry challenges and capitalize on the boom in BTR, single-family construction, connect with Insulfoam’s technical team.