Originally posted in Modern Contractor Solutions Magazine, June 2014 issue
Modern Contractor Solutions Magazine, June 2014 Digital Issue
Three tips for choosing the right material for your project
Which insulation is best for use on buried building foundations and under concrete slabs? Sales reps, naturally, will tell you that their company’s product is best. But, what does independent testing and research say?
These three tips will help your firm select a cost-effective and high-performance rigid foam insulation type for your next below-grade insulation job.
1. CONFIRM LONG-TERM THERMAL PERFORMANCE
Two of the rigid foam insulations most commonly used below grade and under slabs are expanded polystyrene (EPS) and extruded polystyrene (XPS). Although both are closed cell insulations, they perform very differently over the long term.
XPS has a higher initial insulating R-value than does a similar thickness and density of EPS, but the R-value of XPS degrades over time. EPS does not experience such “thermal drift,” and the reported R-value remains the same throughout years of installed service.
This is a crucial point when selecting insulation, as a decreasing R-value means lower thermal performance over time, and thus increased heating and cooling energy and costs for the building owner.
A simple way to confirm an insulation’s long-term thermal performance is to review the warranty. Established EPS manufacturers typically warrant 100 percent of the published R-value for 20 years. By comparison, most XPS warranties typically cover only up to 90 percent of the published R-value, to account for the R-value degradation that occurs in the field.
2. ENSURE MINIMAL LONG-TERM MOISTURE ABSORPTION
In addition to R-value stability, rigid foam insulations differ in their rates of moisture absorption and their ability to dry. Wetted insulation provides lower thermal resistance and can degrade over time. Since insulation installed below grade frequently contacts wetted soil, rates of moisture absorption and the ability to dry is key in these applications.
Independent laboratories have conducted extensive tests of moisture absorption rates for both EPS and XPS. Although XPS often rates better in laboratory short term, fully submerged tests, real-world long term tests show that EPS performs much better. The reason is that EPS has the ability to dry much faster than XPS. This ability to dry at a fast rate helps EPS remain drier during conditions of repeated exposure to moisture.
A 15-year in-situ test of EPS and XPS dramatically demonstrated this point. Stork Twin City Testing evaluated the moisture content of EPS and XPS buried side-by-side for 15 years on a building foundation in St. Paul, Minnesota. At the time the insulations were removed, the EPS was much drier than the XPS—the EPS had only 4.8 percent moisture by volume, compared to 18.9 percent moisture content for the XPS. After 30 days of drying time, the EPS had only 0.7 percent moisture by volume, while the XPS still contained 15.7 percent moisture.
The high moisture absorption rate of XPS in real-world settings is further seen in a 2012 report from the U.S. Dept. of Energy’s Oak Ridge National Laboratory (ORNL). Their researchers found that XPS insulation installed below grade for 15 years had absorbed 67 percent or more moisture.
3. TARGET AN APPROPRIATE COMPRESSIVE STRENGTH
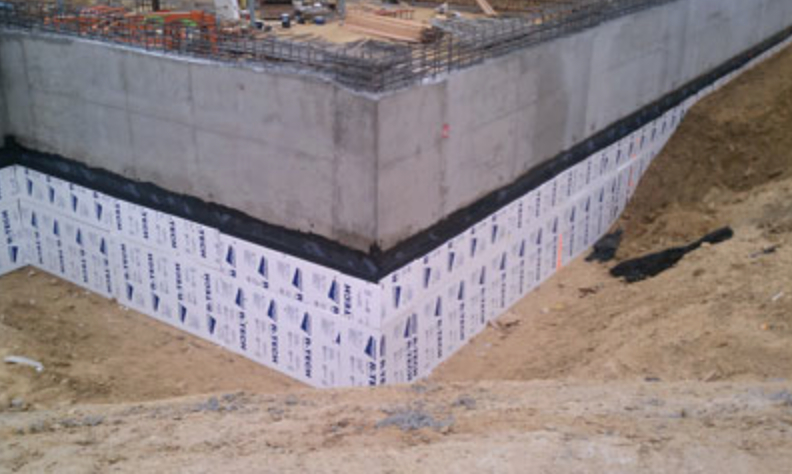
EPS insulation resists moisture better than XPS, including on buried foundations where it is in regular contact with wetted soil.
One of the best ways to save money on rigid foam insulation installed under concrete slabs is to ensure the material is not over-engineered. A common design assumption leads to specification of rigid foam strengths that are many orders of magnitude higher than necessary, which can double the insulation material cost.
Without getting into extensive technical details and mathematical formulas, the problem is engineers often use an overly conservative approach for insulation under concrete slabs. Many designers assume that point loads applied to a slab, such as those from the wheels of a forklift, transfer to the insulation in a triangular load path. Yet, concrete slabs distribute loads more uniformly than this, which means the insulation does not need as high of a compressive resistance as when one assumes a concentrated triangular load path.
An overly conservative design approach often results in specification of a high compressive resistance XPS product, when a more cost-effective EPS would offer sufficient strength. Since XPS typically costs more per inch than EPS, this is wasted money that comes off the contractor’s bottom line.
A simple solution for contractors is to ask the designers if they are using a formula from the Theory of Plates on Elastic Foundations, which take into account how slabs and insulation behave together. A resource to point them to for example calculations is the article “Right-sizing Under-slab Insulation,” in the April 2014 issue of Structure magazine.
CONCLUSION
With building owners’ growing desire to save money on heating and cooling costs, and increasingly stringent energy codes, contractors will be installing below-grade and under-slab insulation on more of their projects. EPS insulation out-performs XPS for both long-term thermal resistance and long-term moisture absorption, and EPS comes in a variety of compressive strengths suitable for nearly all building projects. With the highest R-value per dollar, EPS is the cost effective insulation choice.
Modern Contractor Solutions Magazine, June 2014 Digital Issue
EPS QUESTIONS?
Contact Ram Mayilvahanan, Insulfoam’s Product-Marketing Manager
Ram.Mayilvahanan@insulfoam.com
Connect with Ram on LinkedIn | Follow Insulfoam on LinkedIn